After I removed the main bulkhead, I really started to investigate the core situation of the starboard catwalk. The catwalk was "wet" when I had my survey done in 2016 and had some bounce when walking on it. It was nowhere near soft or spongy, however, and that is due to the incredibly thick outer skin of older Cal boats (contrary to an old C&C 34 I looked at that felt like walking on memory foam).
Construction of my boat consisted of two major phases - lay up the hull and deck as separate pieces, then lift the deck onto the hull and attach. The deck construction is a 1/2" plywood-cored fiberglass sandwich with an inner non-structural skin of about 1/16" and an outer skin of almost 1/4" thick fiberglass. As a result of the deck being fully laid up before being attached to the hull, the upper tabbing of the main bulkhead attaches to the inner non-structural skin of the cored deck. This is plenty strong enough, I'm sure, proven by the long histories of these boats, but it's not as strong as it could be given a slight design change.
Since I am removing the main bulkhead and the coring of the deck, I now have the opportunity to tab the upper section of the main bulkhead directly to the outer skin of the deck, which is almost 1/4" thick fiberglass and where the deck derives much of its structure. I feel that given the opportunity, Lapworth and Jensen would have built the boats this way, except that it is not scalable for a production boat. It requires the deck coring to be glassed in after the deck has already been attached to the hull, which would significantly slow down the two step process I summarized earlier. My design change allows me to have an improved structural connection between the deck and the hull. Generally, this type of design where loads are supported through an object's skin is known as "monocoque" construction. Most sailboats rely on this type of design, however it fails if the connections between the components fail, as can happen when deck core rots. In my case, it will allow me to have a better bond between the deck and the bulkhead, and will also simplify sealing the deck core, as the core will be broken up into discrete segments between bulkheads. I plan to use this approach as I gradually replace all of the core in the catwalks.
To kick this one off, let's start with a video of the deck core near the now-removed main bulkhead.
I began pulling down the core, using the shelf as a handle. Much of the plywood was dripping wet and pulled away from the deck but some remained adhered.
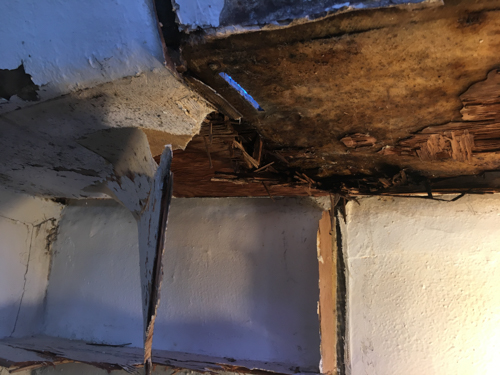
View looking forward. Note the slot for the chainplate to pass through the deck.
After letting parts of the deck continue to dry out and a lot more sanding with a 60-grit disk on my random orbital, I went out and got a a 40-grit sanding flap-disk for my angle grinder. This was a much better tool and made pretty short work of the remaining plywood still epoxied to the underside of the deck.
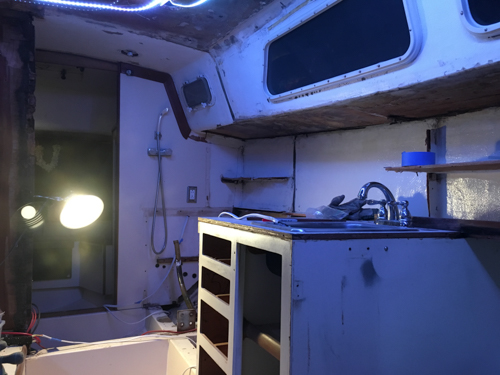
Looking forward. Almost all of the starboard catwalk deck core has been removed.
Next - cutting and installing the new bulkhead!